The WD7015 series is the result of more than 30 years of experience in washing and disinfection for laboratories. It combines the most advanced technologies and reliable solutions in full compliance with current directives and standards (EN15883). The professional Smeg washer-disinfectors are conceived and manufactured with the unique target of ensuring top results in terms of reliability, safety and performances. The innovative system constituted by washer-disinfector, racks and flexible accessories allow the re-processing of a wide range of instruments as well as optimizing spaces and decreasing the end users’ costs. The washing chamber is equipped with the innovative fast coupling system for racks and n. 2 sprayers respectively placed on the ceiling of the chamber and its bottom. The hydraulic system is made of stainless steel AISI 304 with automatic drain at the end of cycle to remove completely all the residuals. The loading is frontal through the drop-down door made of double tempered glass with a vision surface of 82% internal chamber volume. It is also possible to install the optional LED lighting system (optional) into the chamber for optimal visibility. The loading capacity has been increased up to 18 DIN keeping compact dimensions (only 90cm width) and ensuring a usable washing area up to 2.5 m2 depending on the rack.
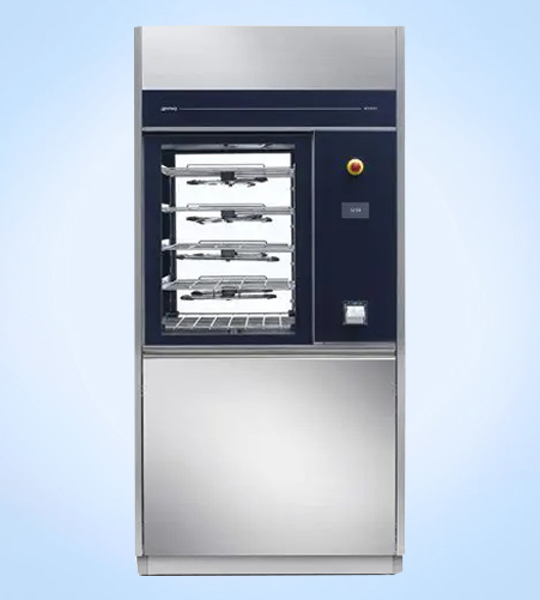
The washing chamber is made of stainless steel AISI 316L, an acid resistant chromium-molybdenum alloy, with rounded edges and sloping surfaces to avoid water stagnation, self-cleaning to remove any risk of bacterial proliferation. The maintenance is easy and safe by accessing to the main components directly from the unclean side of the machine. The washer-disinfector control is entrusted to electronic boards communicating each other (network) to control, display, and monitor all the performed operations in real-time mode by the TFT – 4.3 inches touch-screen with capacitive sensing (on both unclean and clean sides for double-door models). The electronic control system traces each events also in case of power failure. The electronic control system provides a wide range of programs and stores 40 programs in the internal memory, 20 standards and 20 custom.
Furthermore, it is possible to schedule night-time cycles, display all the main parameters in real-time mode such as the achieved A0-value. It is also possible to perform a get a complete diagnostic of the machine. The high precision in dosing of detergents and flow meter control on water intake minimize wastes as well as the environmental impact is remarkably reduced. The electrical consumption has been widely reduced by combining the smart management of the electrical heating, a mindful design of washing cycles and an efficient hot air drying system. The drying system is made of a hot air generator (99.99% DOP HEPA filter) which works in conjunction with the steam condenser for achieving a guaranteed and efficient result. The Smeg washer-disinfectors become even more unique with the WD-CONNECT software for remote controlling and tracing of cycle parameters. The software allows the updating of the machine firmware with no hardware operations, to remotely show and trace all the machine parameters as well as the cycle progress, download the cycles archive for traceability or launch diagnostic functions just by remote
The WD7015 series is the result of more than 30 years of experience in washing and disinfection for laboratories. It combines the most advanced technologies and reliable solutions in full compliance with current directives and standards (EN15883). The professional Smeg washer-disinfectors are conceived and manufactured with the unique target of ensuring top results in terms of reliability, safety and performances. The innovative system constituted by washer-disinfector, racks and flexible accessories allow the re-processing of a wide range of instruments as well as optimizing spaces and decreasing the end users’ costs. The washing chamber is equipped with the innovative fast coupling system for racks and n. 2 sprayers respectively placed on the ceiling of the chamber and its bottom. The hydraulic system is made of stainless steel AISI 304 with automatic drain at the end of cycle to remove completely all the residuals. The loading is frontal through the drop-down door made of double tempered glass with a vision surface of 82% internal chamber volume. It is also possible to install the optional LED lighting system (optional) into the chamber for optimal visibility. The loading capacity has been increased up to 18 DIN keeping compact dimensions (only 90cm width) and ensuring a usable washing area up to 2.5 m2 depending on the rack.
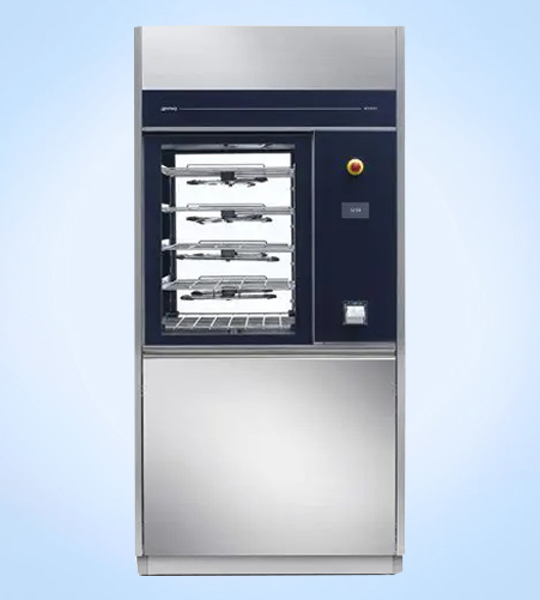
The washing chamber is made of stainless steel AISI 316L, an acid resistant chromium-molybdenum alloy, with rounded edges and sloping surfaces to avoid water stagnation, self-cleaning to remove any risk of bacterial proliferation. The maintenance is easy and safe by accessing to the main components directly from the unclean side of the machine. The washer-disinfector control is entrusted to electronic boards communicating each other (network) to control, display, and monitor all the performed operations in real-time mode by the TFT – 4.3 inches touch-screen with capacitive sensing (on both unclean and clean sides for double-door models). The electronic control system traces each events also in case of power failure. The electronic control system provides a wide range of programs and stores 40 programs in the internal memory, 20 standards and 20 custom.
Furthermore, it is possible to schedule night-time cycles, display all the main parameters in real-time mode such as the achieved A0-value. It is also possible to perform a get a complete diagnostic of the machine. The high precision in dosing of detergents and flow meter control on water intake minimize wastes as well as the environmental impact is remarkably reduced. The electrical consumption has been widely reduced by combining the smart management of the electrical heating, a mindful design of washing cycles and an efficient hot air drying system. The drying system is made of a hot air generator (99.99% DOP HEPA filter) which works in conjunction with the steam condenser for achieving a guaranteed and efficient result. The Smeg washer-disinfectors become even more unique with the WD-CONNECT software for remote controlling and tracing of cycle parameters. The software allows the updating of the machine firmware with no hardware operations, to remotely show and trace all the machine parameters as well as the cycle progress, download the cycles archive for traceability or launch diagnostic functions just by remote
Key Technical Features
The core of new washer-disinfector generation is the innovative electronic system with micro-controllers for controlling each single performed operation as well as for monitoring the overall data stream by means of redundant systems. The Smeg washer-disinfector WD7015 allows to set all the cycle parameters through the multi-language and coloured touch screen display (TFT – 4.3 inches with capacitive sensing) on unclean side and clean side (only for double-door models. In this way, it is possible to set all the washing parameters such as the execution times, the operating temperatures, the detergent amount, the phase number and much more. The access to management operations is protected by a system of 4 password levels.
Control: | Electronic – Network type |
Total programs: | 40 |
Default programs: | 20 |
Custom programs: | 20 |
Display: | Multi-language and coloured touch screen display (TFT – 4.3 inches with capacitive sensing) on unclean side and clean side (only for double-door models) |
Functions: | Temperature, total and residual time, A0-value, ongoing phase, selected program, clock and calendar, reporting of alarm code, maintenance |
Custom phases: | 10 |
Phase parameters: | Water type (cold, hot, demineralized)), detergent amounts, n.2 target temperatures for phase, phase duration, drying time, drying duration |
Displayed temperature range for washing chamber: | From 5 °C up to 95 °C |
Accuracy: | 0.1 °C |
Temperature check: | n. 2 PT1000 probe – IEC 60751 |
The Smeg washer-disinfector WD7015 is based on a closed loop washing system with water intake completely renewed in each phase. The hydraulic system loads 30 L of pre-filtered water, which is drained before the next phase by floor drain (or optional drain pump). The particular shape of washing chamber minimizes the water consumption and ensures the constant pressure in washing circuit. The mixing of additives with water occurs by means of peristaltic pumps inside the washing chamber and in a specific phase of the program. The additives concentration can be set for each program (mixing temperature and detergent dosing can be set for each program).
During the working phase, the washing pumps make the water and additives flow into the sprayer systems. The high rate flow/pressure, in conjunction with temperature and time, allow the removal and dilution of contaminants in the water. The electrical heating system or the optional steam heating system rapidly increases the temperature of water filled in the washing chamber without stopping the circulation and washing processes. The smart management allows loading the water intake in relation to the rack to be used so that the water consumption and waste can be minimized.The water flows into the sprayers placed on the ceiling and at the bottom of the washing chamber as well as into the manifold branches for rack injection or alternatively into the injection systems in relation to the glassware to be processed.
During the heating, the water keeps to flow into the sprayers and the washing process is not stopped. In order to ensure a constant pressure on sprayers and consequently a good quality for cleansing, the machine steadily monitors if the washing pumps work in the best way. The steam condenser, if present, works whenever the water heating generates vapour avoiding leak into the environment. All that means a better glassware drying. Furthermore, the steam condenser avoids the connection to an external air vent.
Filters
Specifically designed for high retention of particles and easy to access for maintenance.
Dosing
The Smeg washer-disinfector WD7015(M) has n. 2 peristaltic pumps for default respectively for dosing the alkaline detergent during cleansing phase and for dosing acidic neutralizer during neutralization phase. Each pump is equipped with its own level sensor placed inside the canister of the used product, with warning on display for empty canister. The dosing precision can be ensured by volumetric flowmeters (optional).
Please refer to the programs table for further details on chemicals consumption.
The detergent compartment is an integral part of the machine on the unclean side; its design is suitable for storing up to 4 x 5 litres and 1 x 2 litres cans. It is equipped with a removable tray for easy cleaning in case of detergent leakages.
"*" indicates required fields